Expository Lump
For relaxation I play music (or least a reasonable facsimile thereof).
The instrument I play is technically known as a "harp-zither," (modeled on a numerical harp-zither) and more usually it's known as a "MacArthur Harp."
To the right is an image of the harp (for this,and all other images,click on the image for a larger view)
An explanation for the terms, you ask?
The "Harp-zither" part is easy -- there are 12 strings (actually steel wires --this is wire-strung harp, rather than nylon-strung) that are parallel to the sound-box (that conforms to the "zither" part). These strings are in diatonic progression from G4 to D6 (that is, from the G above Middle C to the D above the next octave's C) and another set of 12 strings that run from the tuning bridge to the pin-block, and are open to the air (that gives us the "Harp" part) These are in three groups of 4, grouped for use as chords, rather than in direct progression. The diatonic scale is continued from F4 down to F3 (that is, the F above middle C to the F below middle C.
Then there is that "numerical" description. Well, when the original of this was first produced and sold, there were numbers pasted on the tuning bridge, and the owner could "play by number" using music sheets that had the numbers written-in, so the player really didn't need to be able to read "normal" music. It's an idea that is still in use for some instruments.
It's also known as a "MacArthur Harp" after the late Margaret MacArthur, who was a folk song collector and preserver. She had received a (somewhat broken) example of this little harp in 1961, her husband restored it and she used it during her concerts and on her recordings.
My example was built by Keith Young, who is still a practicing luthier. I bought it the year it was made, in 1988 (the label in the sound hole has an identifying number of "M-16") and have been playing it since. Yes, I have a musical instrument that is old enough to drive, vote and legally imbibe Adult Beverages.
However, like most wooden musical instruments, the way parts are joined is usually just by the shape and fit (think variations on the dovetail joint you find in some furniture and in some house construction) and glue. As these instruments age, and especially as they are played, the tension of the strings (which, after all, is what helps determine the note to be played) puts stress on the parts of the instrument where the strings are attached to the body. In a harp of this sort, the stressed parts are the pin-block (at the bottom of the picture, where the wire strings are anchored) and the tuning bridge (the curved structure at the top, where the other end of the strings are threaded through a tuning pin which is adjusted to lessen or increase the tension on the string*.
Pin block
this shows the pin-block, and the anchor pins. The strings at this lower end either pass over the lower bridge (for the zither portion of the string set) or through holes drilled in the bridge itself (for the harp portion of the string set)
Tuning bridge
This shows a portion of the tuning bridge for the higher notes for the instrument. The strings are threaded through a hole in the tuning peg, and the peg is adjusted to decrease or increase the string tension.
In the case of my little harp, the glue in the pin-block was failing, and the string tension was causing the pin-block to rotate away from the instrument back. The first symptoms I saw were that the instrument was always going "flat," and I had to continually tighten the strings back up to the proper tension (as the pin-block was rotating out away from the instrument back, the distance between the anchor pins in the pin-block and the tuning pins in the tuning bridge was shorter, and the corresponding tension was lower, which lowered the frequency of the note produced). The next symptom noticed was that there was a visible gap where the block was separating out.
Being neither a woodworker nor a luthier, I just let things go, until I had no choice but to act. I reasoned that, since this kind of repair would involve partially disassembling the instrument and regluing, the repair cost would likely exceed the cost for a new instrument. I contacted Keith Young by e-mail to ask if he had used hide glue or not (the use of hide glue is common for many luthiers). He said he had not, as he found that the glue did not last as well in the kinds of tensions found in these instruments. I decided that I would use a commercial glue with the brand name of "Gorilla Glue" (prior use of this brand had given my good results in the little wood gluing I had done in the past) for the repair.
Break-down
First thing I had to do was to take the strings off the harp (some had not been replaced in the 21 years I had had the instrument, other had been replaced as often as twice a year). For some of the strings it was a matter of simply unwinding them from their tuning pegs, unthreading from the post and lifting from the anchor pegs. (I don't have any pictures of this phase, because I didn't think to document with pictures until after the dis-assembly had already begun)
Others had to be cut off (I did mention that some strings had been on the harp for two decades), because they were simply too well-coiled on the posts to easily unthread, and would just break if I tried to reuse them.
The plan was to break down the harp, lightly sand all the glued surfaces, repair spacer blocks, re-glue and clamp.
Once the strings were removed, I used a heat gun (cleverly disguised as a hair dryer) and a spray bottle of water to separate the pin-block and support post. The combination of heat and moisture was what was needed to make the glue lose its bond with the wood.
I was able to break the ties that bind and take off the pin-block and the support post (the turned wooden column shown to the left of the body. As mentioned above, I was going to remove the back of the soundbox as well, and more firmly attach the spacer blocks (the interior blocks that keep the front and back of the soundbox from collapsing together.). However, that plan went south when, partway through the dis-assembly of the instrument back, it turned out that, even with the glue softened, the glue was still stronger than the wood of the soundbox, and the wood started to split outside the glue area. So I stopped the process at that point and didn't try any further breakdown.
Disassembled
The picture to the left shows the harp in its disassembled state. The support post is at left, the pin-block is shown separated from the body.
Not shown is the lower bridge. Neither the lower nor upper bridges are glued on, but held in place with small diameter flat-headed nails. The nail holes for the lower bridge can be seen on the soundbox.
The maker's label can be seen through the sound hole.
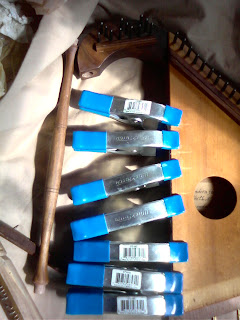
Re-glue the box
Because I had partially disassembled the soundbox, before anything else, I had to re-glue those pieces so everything was tight before I tried to put the pin-block back. I sanded the areas that I could reach to remove as much of the old glue residue as I could, ran a damp paper towel over the sanded surfaces to catch as much of the dust and residue as I could, applied the new glue and clamped surfaces.
The pin-block and lower bridge can be seen to the left of the body in this image. (Did I use enough clamps?)
.
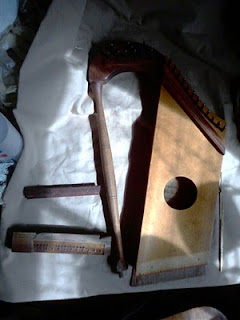
Reset Post
Next step was to reset the support post. This post slots into a hole in the pin-block, and serves the dual function of providing a support brace against the tension of the metal strings and also provides a handle while playing.
The pin-block and lower bridge can be seen to the left of the harp, the brass rods on the right fit into the bridges and the strings rest on them, rather than on the wood of the bridge.
Finished!
The same clamps, with the addition of straps for vertical stability, were used when the pin-block was set in place. (Sorry no pic of that) But we do have the picture of the harp. rebuilt, before restringing.
And this video gives a sample of what my little girl sounds like. This was just a quick capture to show what the harp sounds like after the rebuild (actually, it sound like it did *before* the rebuild, but it holds tone better now.
==========================================================
*The tension on these strings can be, well stressful (as an example, one string that can be used on a bass mandolin has a tension range from 59 pounds (when tuned to C') to 236 pounds (when tuned to C) ). Imagine now that the tension is constantly being applied between the two attachment points.
You can see that, eventually, Something Has To Give. Ideally, the wear on the instrument can be lessened by either removing the string entirely or loosening the string to slack, both of which remove the tension. However, this puts the strings through mechanical fatigue as the strings are manipulated to slacken them, and then tighten to bring back to the correct tuning. This fatigue is especially acute in metal strings, as metal is very brittle when subjected to that repeated stress.